Fill Finish
Background
AVS Life Sciences delivers cutting-edge engineering, projectmanagement, automation, validation, and clinical solutions to clients in the pharmaceutical, biotech, medical device, and diagnostic industries. Our team goes beyond execution—we build lasting partnerships and ensure full traceability in every service we provide, from utilities support and preventive maintenance to installation and documentation.
We are proud of our 100% success rate across FDA, EMA, and PIC audits, a testament to our rigorous quality and compliance standards.
In this case study, we detail a complex, multi-year collaboration with a major pharmaceutical manufacturer to repurpose an underutilized room within an activeGMP facility—ultimately enabling a new continuous direct compression manufacturing process.
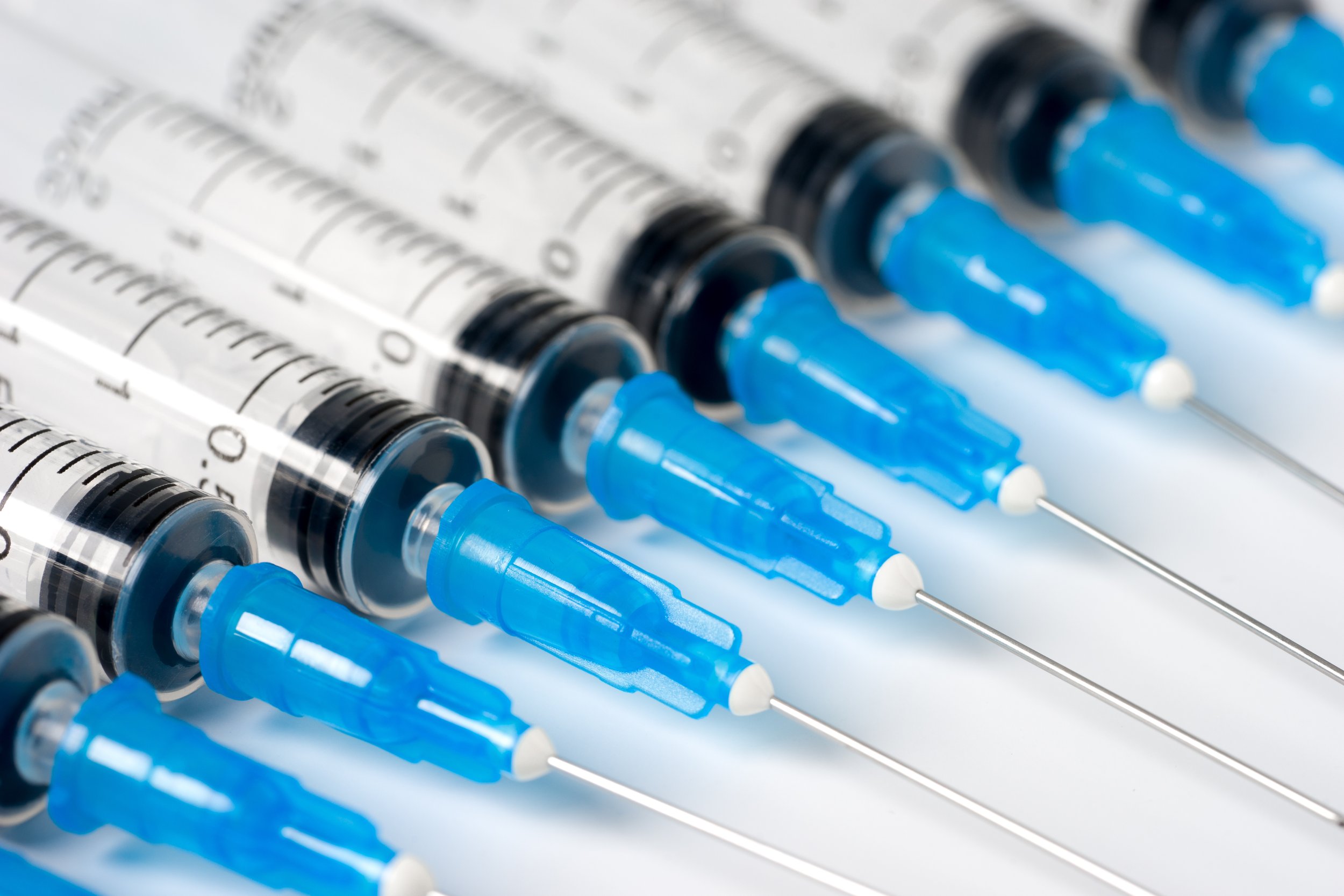
The client is a biotech company based in Taiwan that manufactures vaccines. The target audience is Biotech and Pharma.
- The client wanted to expand their fill/finish facility and add a new high-speed pre-filled syringe filling and packaging line.
- The fill/finish facility was originally designed and built for one syringe line and one vial line.
- The new syringe filling and packaging line will be used to manufacture three different vaccines, one of which is under contract for a large multinational vaccine manufacturing company.
- Facility and clean utility modifications had to be carried out to accommodate the new filling and packaging line, along with new process equipment including formulation and buffer preparation tanks, Clean-in-Place (CIP) system, syringe transfer and disinfection system, debagger, syringe filler, isolator, de-nesters and re-nesters, syringe inspection machine, plunger rod insertion and labeling machine, thermoforming machine, cartoner, case packer, and drug traceability serialization system.
- The client required AVS project management skills, fill/finish knowledge and expertise to provide
- Design services for facility Basic Design (BD), process Detail Design (DD), commissioning and qualification services for the new high-speed syringe filling and packaging line.
- Conducted Basic and Detailed design review meetings to create multi- disciplinary drawings that meet the client requirements.
- The Basic Design services included the engineering design for architectural, building mechanical, process mechanical, process instrumentation, process automation philosophy, piping, material handling/logistics, and electrical requirements.
- The Detailed Design services included the Formulation, Buffer Prep., and CIP processing systems and piping requirements.
- Reviewed and revised Validation, Cleaning Validation, and Process Validation Master Plans for the new high-speed syringe packaging line.
- Prepared User Requirements Specifications (URS) for syringe secondary packaging equipment including plunger rod insertion
- and labeling machine, thermoforming machine, cartoner, case-packer, and drug traceability serialization system.
- Prepared impact and risk assessments for syringe packaging equipment, buffer preparation system, formulation system, and CIP system.
- Prepared and executed Design Qualification (DQ), Installation and Operational Qualification (IOQ) Protocol for Formulation system and PFS Filling and Packaging Equipment.
- Successfully procure the process equipment that meets their needs with the URS prepared by AVS and the drawings prepared from BD and DD.
- Successfully qualify all process equipment for the new high-speed pre- filled syringe filling and packaging line.
- Successfully complete the expansion project for the new syringe filling and packaging line on-time and within budget.