AVS Life Sciences provides full-service biopharmaceutical drug development services spanning from drug discovery to commercialization and quality monitoring.
Biopharmaceutical
Drug Development
AVS provides lifecycle support in GxP Quality, Regulatory, Commissioning, Qualification, and Validation
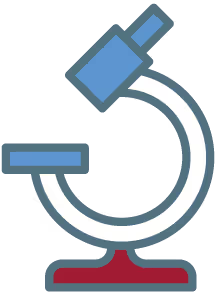
Drug Discovery
Identifying and characterizing molecules to safely treat diseases is a complex, resource-intensive process requiring interdisciplinary collaboration. Pre-clinical safety studies, conducted before Phase 1 trials, assess a drug candidate’s safety, biological activity, and potential efficacy through lab tests and animal models.
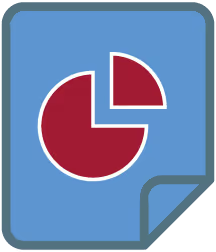
Pre-Clinical Safety Studies
Preclinical studies are performed in in vitro, in vivo, ex vivo, and in silico models to obtain basic information about the safety and biological efficacy of a drug candidate before testing it in a final target population, i.e., humans. Preclinical studies or tests are mainly performed in compliance with GLP/GSP guidelines (good laboratory practice and good scientific practices) to ensure reliability and reproducibility of results. The FDA/EMA require supporting basic preclinical data to IND application especially on toxic effects, safety profile, pharmacokinetics, and pharmacodynamics.
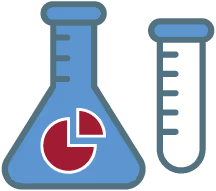
Early Formulation Development
Early formulations are prepared mostly for drug compounds at both discovery and preclinical stages and are used to animals via various routes such as oral and intravenous dosing. They serve the purpose of evaluating these compounds on a broad range of pharmaceutical interests, notably pharmacology (activity/efficacy), pharmacokinetics (PK), and toxicology.
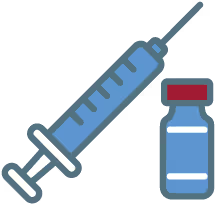
Clinical Trials (Phase 1–4)
Clinical trials are often conducted in four phases. The trials at each phase have a different purpose and help scientists answer different questions:
- Phase I: Dose-ranging on healthy volunteers for safety and tolerability
- Phase Il: Testing of drug on participants to assess efficacy and side effects
- Phase III: Testing of drug on participants to assess efficacy, effectiveness, and safety
- Phase IV: Phase IV clinical trials happen after the FDA has approved medication. This phase involves thousands of participants and can last for many years.

Technology Transfer
The goal of technology transfer activities is to transfer product and process knowledge between development and manufacturing, and within or between manufacturing sites to achieve product realization. This knowledge forms the basis for the manufacturing process, control strategy, process validation approach, and ongoing continual improvement.
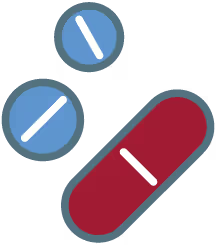
Manufacturing Process
A manufacturing process is a series of steps involving machinery, devices, and labor to convert raw material into finished goods. The process also must have set norms, such as tolerances, quality measurements, and performance metrics. Pharmaceutical manufacturing is the process of industrial-scale synthesis of pharmaceutical drugs as part of the pharmaceutical industry. The process of drug manufacturing can be broken down into a series of unit operations, such as milling, granulation, coating, tablet pressing, and others.
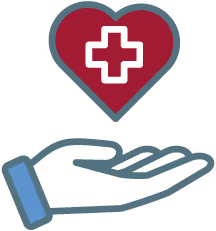
Commercial & Quality Monitoring
In the pharmaceutical industry, commercialization refers to the process of bringing a new drug or therapy to the market and making it available to patients. It involves various activities such as regulatory approvals, distribution, marketing, and sales. Quality monitoring is essential for ensuring product quality and patient safety after regulatory approval to ensure continued safety and efficacy of marketed products.
Services
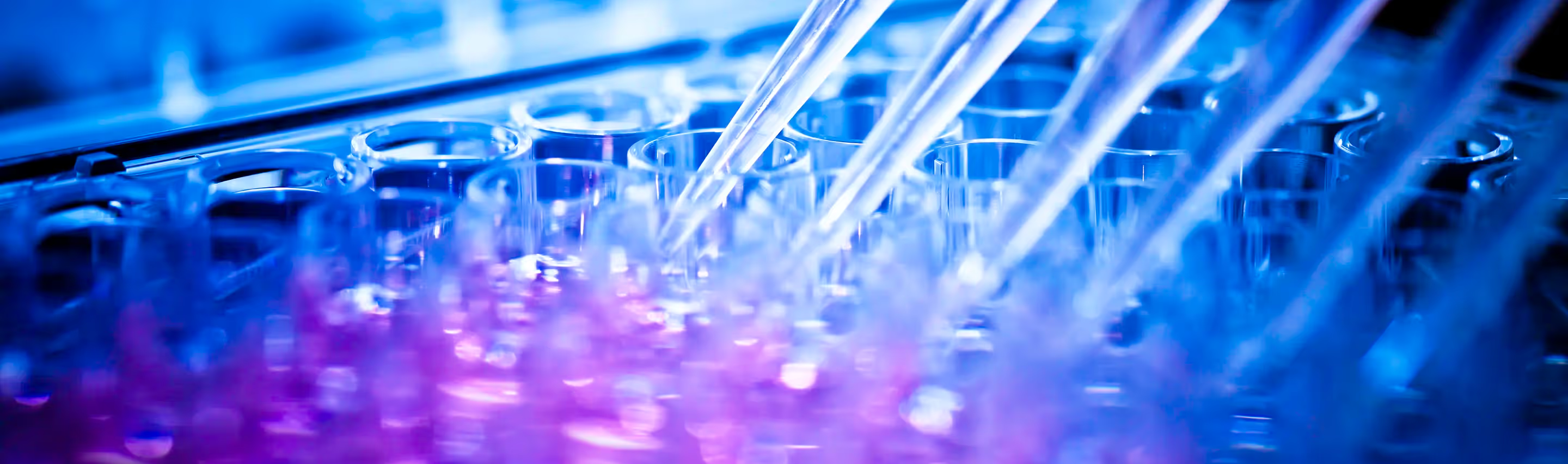
Our end-to-end biopharma services support each stage of biopharmaceutical development to ensure quality and regulatory compliance. By facilitating each phase of the drug development process, we create a seamless solution refined to each client's needs.
- Analytical, QC, CMC & Regulatory Affairs
- Batch Review and Disposition
- Change Control
- Clinical Operations
- Clinical Study Reports (CSR), Protocols, Informed Consent Forms (ICF)
- Complaint Handing Support
- Compliance Audits & Gap Assessments
- Design & Review Case Report Forms (CRF)s & electronic CRFs (eCRF)
- Document Development (SOPs, Policies, Forms, Technical Documents)
- Drug Master File (DMF) Preparation
- Environmental Monitoring Program Development
- FDA Strategies
- GXP Training
- Health Authority Assessment and Remediation
- Inspection Readiness and Audit Support
- Interim Quality Leadership
- IT Systems Support & Implementation (QMS, ERP, MES, etc.)
- Lab, Clinical, and Scientific Operations Support
- Lab Instrument, Software Systems, Network Validation
- Manufacturing Compliance Oversight
- Manufacturing Engineering
- Manufacturing Support
- Medical Writing and Regulatory Submissions: INDs, NDAs, CTD/eCTDs, BLAs, IB, etc.
- Methods Development
- Packaging Engineering & Validation
- Part 11 Compliance
- Project Management
- Protocol & Report Writing/Editing
- Quality Control
- Quality Event Management (Deviations, Investigations, CAPA implementation)
- Qualification Support for Pilot Plant Facilities
- Quality Strategy Development, Implementation, And Management
- Quality Management Systems Development & Implementation
- Review Monitoring Plans, Communication Plans, Data, & Reports
- Validation: Cleaning, Equipment, Process, Software
Our quality and regulatory services cover the entire biopharmaceutical lifecycle. We ensure that your systems, processes, teams, and facilities remain compliant with shifting regulation and the highest industry standards.
GCP Audits:
- Investigator Sites
- Sponsor Audits & PAI Preparation
- CROs
- Clinical Labs
- BIMO
- TMF
- GDP
- Safety Surveillance/Pharmacovigilance & Complaint Handling Sites
- DMPK & Bioanalytical Labs
GMP Audits:
- API & Drug Product CMOs
- Contract Test Labs
- Manufacturing, Storage, & Distribution Sites
- Data Integrity
- Animal Test Facilities, Bioanalytical, CAP/CLIA
GLP and GLCP Audits:
- Animal Test Facilities, Bioanalytical, CAP/CLIA
Information Technology Audits:
- CSV, SDLC, Part 11 ComplianceGMP-API & Drug Product CMOs, Contract Test Labs, Manufacturing, Storage, & Distribution Sites, Data Integrity
- GLP and GLCP Audits
- Information Technology: CSV, SDLC, Part 11 Compliance
- Qualification, For Cause, etc.
Qualification/Requalification, Supplier, For Cause Audits, etc.
- FDA-483, Warning Letter Response & Remediation
- Inspection Support & Facilitation
- Mock GXP Regulatory Inspections
- BLA, NDA, ANDA, etc. Submissions
- Pre-Approval Inspection (PAI) Readiness Preparation & Planning
- Sponsor, CRO, CMO Training & Readiness
GXP
- Data Integrity
- Deviations, Investigations, & CAPA
- FDA Regulations (GCP, GLP & GMP)
- Great Documentation Practices Standard Operating Procedures (SOPs) Development
- Interacting with FDA
- Internal & External Auditing Techniques
- Managing Quality in a Virtual Company CFR Part 11 Compliance
- Technical Writing
GCP
- Clinical Monitoring Techniques
- GXP Sponsor Responsibilities
- Oversight of Clinical Service Providers
GMP/GLP
- Aseptic Techniques
- Equipment Qualification
- FDA QSIT (Quality System Inspection Technique) Audit Approach
- GMPs in Research & Development
- HACCP (Hazard Analysis & Critical Control Points)
- Out-of-Specification (OOS) Issues
- Overview of Methods Validation
- Packaging & Labeling GMPs
- Validation
- Analytical Methods Validation
- Automation Validation
- Cleaning Validation
- Cold Chain/Shipping Qualification
- Computer Systems Validation (CSV)
- Decommissioning
- Development Testing
- FAT/SAT Testing
- Facilities/Equipment/Utilities (FUE) Validation
- Information Technology Validation
- Packaging and Shipping Validation
- PLC Control Serialization (track & trace)
- Process Validation
- Validation Maintenance
- Construction Project Management for GMP
- CQV Project Management
- Engineering Project Management for GMP
- Life Cycle Management
- Quality Change Control Management
- Risk Assessment and Risk Management
- Startup and Commissioning Coordination
- Vendor Procurement and Management
- Asset Management / ERP Master Data Generation
- Maintenance Strategy Management
- Quality Engineering
- Reliability Engineering
- Spare Parts/Instrumentation P&ID Verification
Get Started with AVS Life Sciences
Ready for best-in-class service? You can count on our team of industry-leading professionals to deliver the solutions you need. Contact us today!
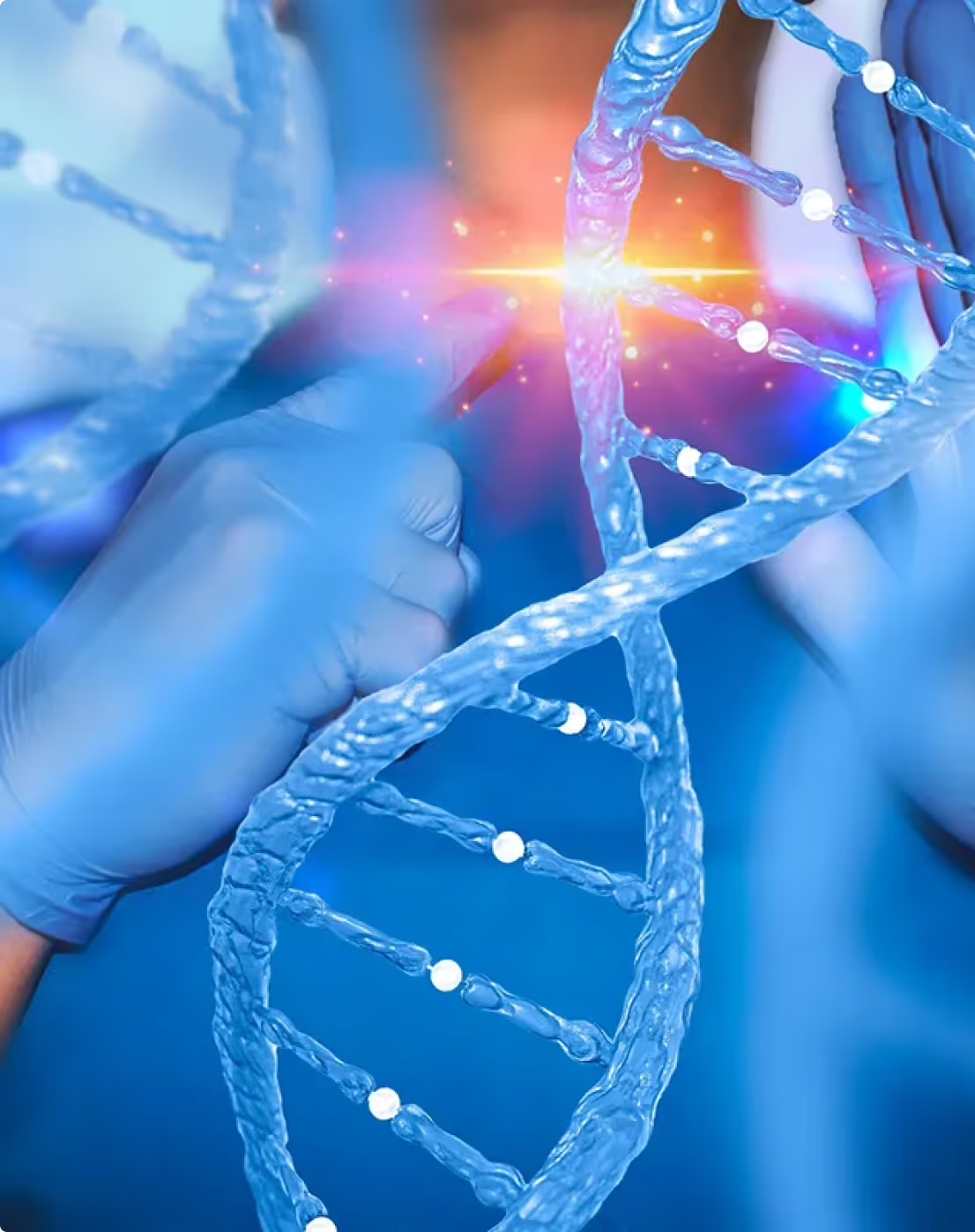
Cell & Gene
Therapy
This manufacturer was using a multi-product Biosafety Level 1 GMP facility throughout their product and process development. The facility was used to manufacture drugs intended for phase 1 and 2 clinical trials.
While this Level 1 facility provided the client’s desired functionality at the time, they wanted to manufacture lentivirus vector material. To fulfill this goal, our client needed to upgrade their manufacturing facilities to be compliant with Biosafety Level 2 GMP standards, a requirement for this material.
This Cell and Gene Therapy project required AVS’s support to guide the client’s engineering, validation, and technician groups to modify the Level 1 facility, and install, commission, and qualify the new equipment within 9 months.
DIVIDED INTO 2 PARTS:
1. Modify the existing facility
2. Install, commission, qualify new equipment, and prepare preventive maintenance
AVS collaborated with the client to enhance their manufacturing facility by conducting a gap analysis that revealed differences between the current setup and the required Level 2 facility. A new layout was created and approved, followed by equipment procurement, where AVS managed vendor communications and documentation. AVS guided the installation of complex equipment, conducting commissioning protocols to validate functionality across over 80 new pieces of equipment. The process included qualifications (IQ/OQ/PQ) and computer system validation to meet GMP standards. After installation, AVS developed preventive maintenance plans and handed off the documentation to the client. Throughout the 9-month project, AVS maintained clear communication, managed task delegation, and held monthly budget review meetings with client leadership to ensure on-time, on-budget delivery.
AVS assisted our client in upgrading their manufacturing space from a Biosafety Level 1 GMP facility to a Level 2 GMP facility. We were able to complete the entire project on schedule and within budget. Moreover, our documentation efforts to demonstrate full traceability was deemed appropriate by our client’s quality assurance team. We were able to support our client throughout this entire transition process, from gap analysis to final equipment installation. Because of our efforts, this pharmaceutical manufacturer was able to manufacture medication with the lentivirus vector material. This collaboration allowed our client to focus on what they do best – develop medicines to help improve their target patient’s quality of life.