Cell & Gene Therapy
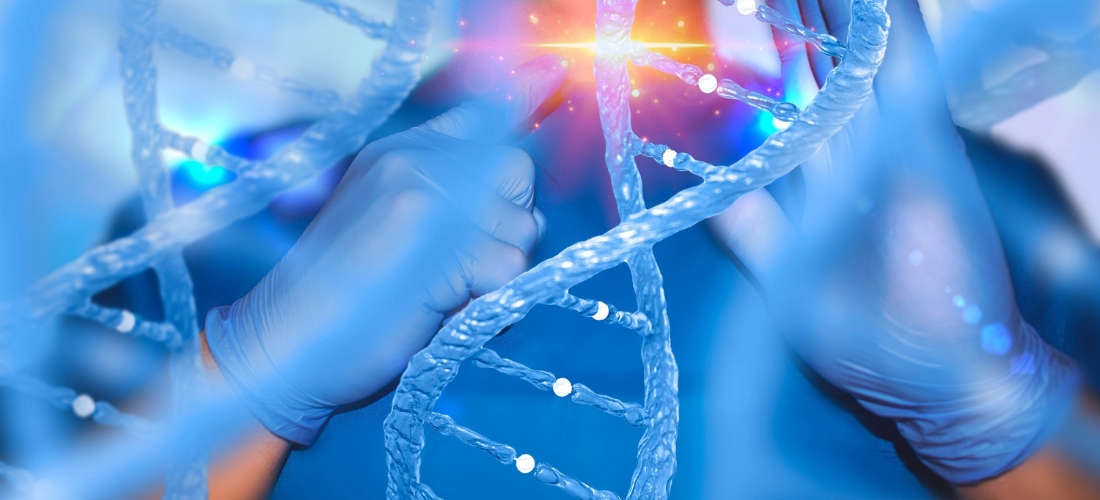
This manufacturer was using a multi-product Biosafety Level 1 GMP facility throughout their product and process development. The facility was used to manufacture drugs intended for phase 1 and 2 clinical trials.
While this Level 1 facility provided the client’s desired functionality at the time, they wanted to manufacture lentivirus vector material. To fulfill this goal, our client needed to upgrade their manufacturing facilities to be compliant with Biosafety Level 2 GMP standards, a requirement for this material.
This Cell and Gene Therapy project required AVS’s support to guide the client’s engineering, validation, and technician groups to modify the Level 1 facility, and install, commission, and qualify the new equipment within 9 months.
DIVIDED INTO 2 PARTS:
- Modify the existing facility
- Install, commission, qualify new equipment, and prepare preventive maintenance
To tackle the first challenge, AVS met with our client to fully understand their manufacturing capabilities and needs. Through these conversations, the joint team (an engineering firm and our client) created a plan to modify the existing facility with a gap analysis. This gap analysis clearly showed the differences between the current facility and the needed Level 2 facility.
Once we were aware of these gaps, the team drafted a schematic of the desired Level 2 facility layout. Following approval, the engineering team submitted requests to purchase the necessary equipment. AVS assisted with this equipment procurement process as the primary contact for equipment vendors, ensuring that they would provide all the required documentation per our client’s procedures.
Once the equipment arrived on site, AVS guided the installation process, along with our client’s manufacturing team. Since this was complex equipment, we needed to perform a commissioning process with more than a dozen different pieces of equipment to demonstrate and document that the equipment was suitable for their processes. AVS prepared and performed the commissioning protocols for our client.
After commissioning, we drafted the protocols and performed installation, operational, and performance qualifications (IQ/OQ/PQ) on all 80 new pieces of equipment. This qualification process included computer system validation to adequately prepare the facility for system control and appropriate GMP data storage.
Finally, AVS provided installation support and drafted preventive maintenance plans for our client. After successful equipment installation, we passed these documents to our client with the preventive maintenance instructions.
Throughout the entire project, our engineers clearly communicated with the client and their contract staff to ensure that tasks were appropriately assigned, while monitoring their schedule and budget over the 9 month collaboration. To further monitor the budget, our site lead conducted monthly meetings with our client’s upper management team to review metrics. This allowed us to mitigate schedule and budget modifications.
AVS assisted our client in upgrading their manufacturing space from a Biosafety Level 1 GMP facility to a Level 2 GMP facility. We were able to complete the entire project on schedule and within budget. Moreover, our documentation efforts to demonstrate full traceability was deemed appropriate by our client’s quality assurance team.
We were able to support our client throughout this entire transition process, from gap analysis to final equipment installation. Because of our efforts, this pharmaceutical manufacturer was able to manufacture medication with the lentivirus vector material. This collaboration allowed our client to focus on what they do best – develop medicines to help improve their target patient’s quality of life.