Batch Processing Integration
Background
AVS Life Sciences delivers cutting-edge engineering, projectmanagement, automation, validation, and clinical solutions to clients in the pharmaceutical, biotech, medical device, and diagnostic industries. Our team goes beyond execution—we build lasting partnerships and ensure full traceability in every service we provide, from utilities support and preventive maintenance to installation and documentation.
We are proud of our 100% success rate across FDA, EMA, and PIC audits, a testament to our rigorous quality and compliance standards.
In this case study, we detail a complex, multi-year collaboration with a major pharmaceutical manufacturer to repurpose an underutilized room within an activeGMP facility—ultimately enabling a new continuous direct compression manufacturing process.
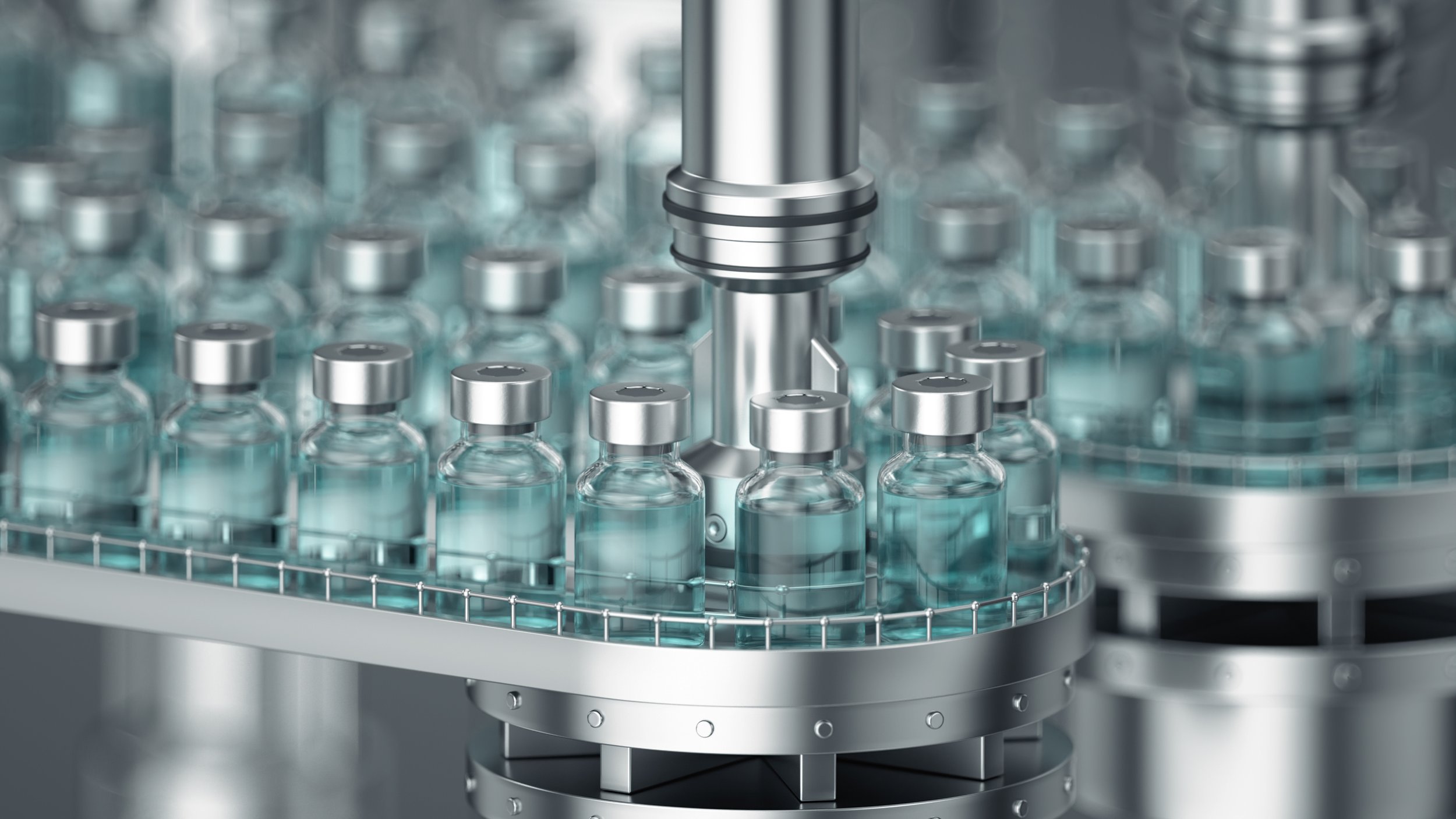
The client is one of the largest pharmaceutical companies in the world. They provide healthcare solutions to over 170 countries worldwide.
- The client built and commissioned a vaccine manufacturing facility. As part of the original qualification and commissioning of the facility, a large part of the automation and IT components were excluded from the scope.The fill/finish facility was originally designed and built for one syringe line and one vial line.
- The HMIs and PLCs that control all the equipment were all stand alone and there was very little information being passed across facility from area to area.
- Operators and engineers were not able to access any historical data which made any deviation investigations challenging.
- Many deviations led to discarding any questionable batches because the client didn't have a way to vary the product, which became in scope after the fact.
- The client required AVS expertise in automation and system integration to implement a solution that can better leverage the clients existing site network infrastructure.
AVS proposed a 3 phase plan to improve the facilities IT capabilities which would ultimately reduce and make it easier to resolve any deviations.
NETWORK INTEGRATION
Connect the 30 or so PLCs and 15 HMIs to the existing site wide industrial network. This network was used in other facilities within the site for the purpose of industrial network communications.
DATA COLLECTION
Designed, qualified, and validated 2 redundant servers whose purpose was to collect the data from the PLCs via OPC Communications over the industrial network protocol (which was integrated in phase 1), and transfer that data to the site wide Pl data historian. The reason there was 2 servers instead of 1 is to allow complete redundancy in the case either server fails, with no impact to the data collection.
BATCH REPORTING
With the data gathered in the 2nd phase, AVS worked with the client to design, qualify, and validate End of Batch RtReports. This allowed the operators within the facility to have a consolidated report with all key process parameters defined. SOPs and training documents on the use of PI Historian and RtReports were also developed by AVS.
The integration of the vaccine manufacturing automation system to the site wide industrial network created value for the client in the following ways:
- The HMIs were now able to get periodic windows patches and security updates without having to be taken out of service and manually patched/updated.
- The operators now used network accounts to access the HMIs rather than use local unmanaged accounts. Access and password management became managed by the IT team rather than by the facility managers and operators who can now focus on what they do best which is make vaccine.
The PI data collection created value in the following ways:
- Data Gathering Time: With the data now available in Pl, operators and facility managers will know if any building equipment is or was operating out of spec in fractions of the time it took prior to the data being collected electronically. Users can now see the data anywhere in the world with an internet connection rather than having to go to the production floor to view the data.
- Deviation Investigation: One of the biggest costs to the client was discarding of deviated batches. Each discarded batch costs the client over $1 million in sales. With the historical data now being collected in Pl data historian, data can easily be gathered which supports any deviation investigation. This data has since been attached to 100s of deviations which did not lead to discarded batches.
The Reports created value in the following ways:
- The reports have saved the client considerable man hours as the operators don't need to manual record all the parameters or pull chart recorders for each batch.
- It also made the release of the product easier on the team that reviews the data as only the pertinent data is presented in these reports.
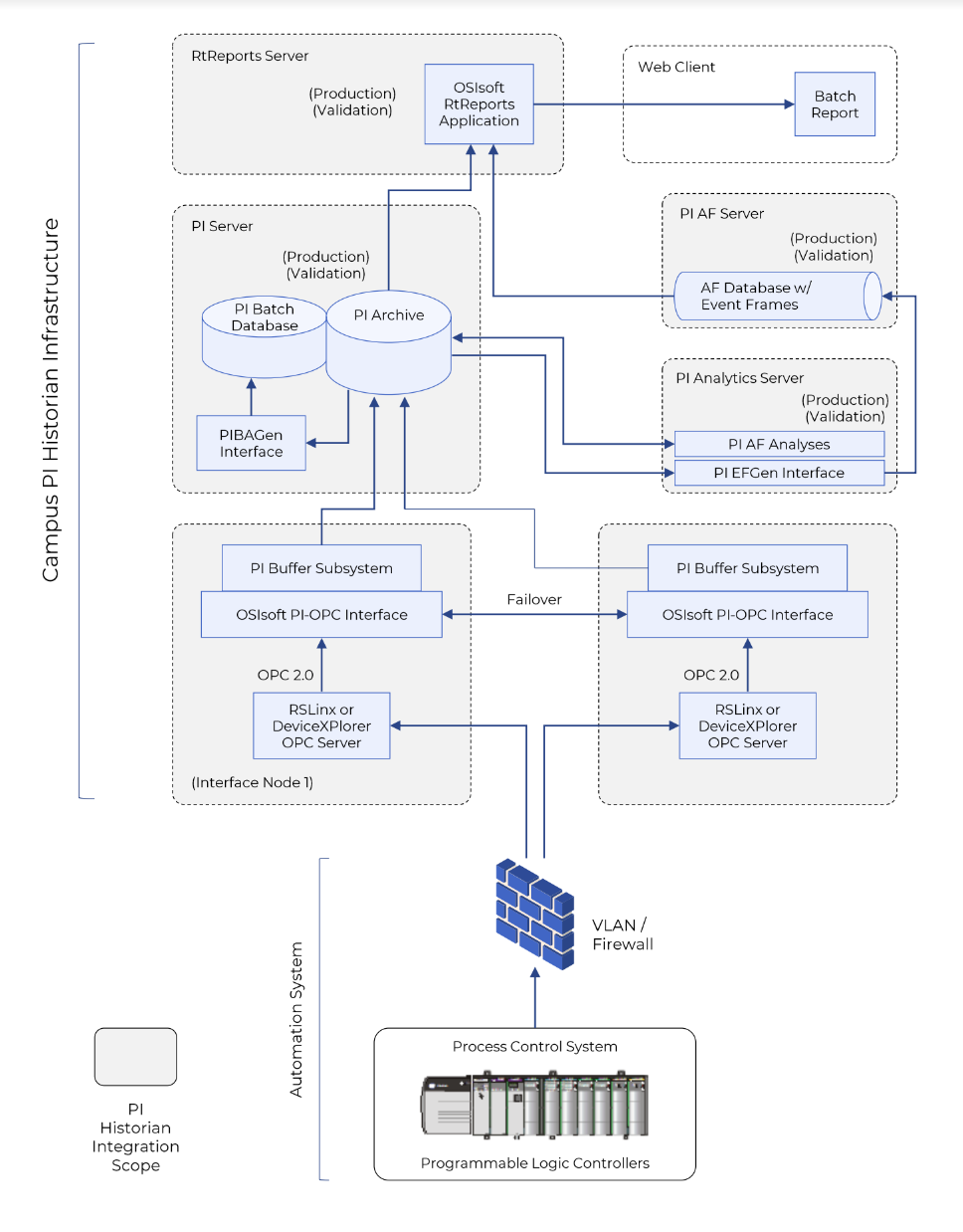