Life Sciences Start-Ups: What You Need to Know About Phase Appropriate Quality Requirements
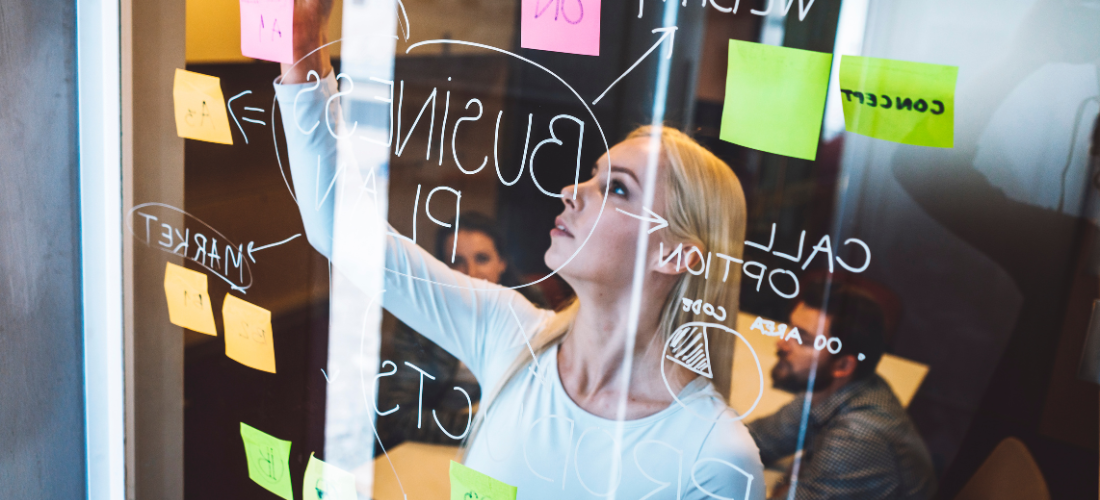
Whether your start-up company makes pharmaceutical products, biologics, or medical devices, you all have one thing in common. You need to implement a robust digital quality management system (QMS) at the early phase of product development to comply with the ever-changing and more stringent regulations throughout the product life cycle. A well-designed digital QMS ensures high quality products are manufactured, challenges are managed appropriately, and all personnel are properly educated and trained to perform their functional tasks as appropriate. Remember you use this data to make critical decisions on whether to move forward with your programs, so the data must be compliant and demonstrate data integrity when submitted to any regulatory agency.
Numerous Documentation Requirements
Phase appropriate means to develop your QMS with policies, procedures, and controls applicable to the phase of development of your product. Many start-ups make the mistake of waiting to do this until they are in late phase product development. By implementing a phased approach early enough and using a digital QMS, a company can increase compliance and reduce the costs of establishing a QMS. This means a company starts with a standardized document philosophy that evolves with each phase of documentation requirements, which all support investigational new drug applications (INDs) and GxPs to maintain a robust QMS These documents include:
- a Quality by Design (QbD) Philosophy.
- quality policies.
- document control and retention.
- standard operating procedures (SOPs).
- training records.
- subsequent documentation of manufacturing and testing batches (batch records).
- supplier qualification documents.
Increasingly Complex Documentation at Each Phase
When in early R&D stages, companies tend to use lab notebooks to document their work and opt to use paper systems. Managing a small volume of documents manually may appear to have advantages such as a faster time to start a study, and not committing to an electronic system too soon, but using a paper-based QMS has more disadvantages in the long run.
As the product moves through its lifecycle, additional procedures are required to ensure safety and compliance for the patient, making management of the paper documents labor intensive to print, scan, and file; requiring more space for filing hard copies; and routing of documents for approval being more time consuming with greater potential for lost documents.
Overall, this increases the risk for proper documentation genealogy when putting all the pieces of the puzzle together a few years later when preparing your submission to regulatory agencies. The necessary documentation also includes training records, and if you are using a manual, paper-based process, ensuring training completion by using Excel spreadsheets, emailing employees, etc. results in extra time to track current training and reporting compliance metrics for each employee. This outdated approach presents an additional risk to overall compliance with cGxP requirements.
Once a company decides to move to Phase 1 clinical trials, it is critical to comply with the regulations specific to manufacture Phase 1 clinical products, which is a subset of the full cGMPs, and they ensure patient safety, product quality, and data integrity. From the start of Phase 2, and continuing through commercialization, products must be in compliance with the full set of cGxP regulations, which requires management and storage of a large volume of documents.
Manage Documentation & More With a Digital QMS
Today’s digital QMS is secure, 21 CFR Part 11 compliant, and available for purchase at a reasonable cost. They typically include document management, training, deviation, corrective action/preventative action (CAPA), change control, complaints, etc. with additional modules that can be added when they are needed. Most of these are scalable and can allow your company to be up and running within two months or sooner (after contracts are approved), provide full validation protocols, and can ease the burden of manual document routing/approval/retention, and manual tracking of cGxP documents. In addition, data can be easily imported to another system should you need to change to a different service provider in the future.
A Phase Appropriate Digital QMS Eliminates Headaches & Saves on Costs
The negative consequences of not implementing a phase-appropriate digital QMS in the early phases are numerous. You might jeopardize compliance, risk patient safety and product quality, lose critical documentation to support regulatory submissions, and encounter data integrity issues due to poor documentation practices, all of which can negatively impact your company’s success. It is also much more costly to convert from paper to a digital system in later phases of the product lifecycle.
Given the appropriate design and level of complexity based on your company’s structure, a digital QMS system could be your most efficient and compliant solution to get your product to approval and improve the lives of your patients.
In summary, implementing a digital phase appropriate QMS early in your product development life cycle will help you avoid many of the mistake’s startup companies experience. It ensures your documents are managed properly with version control and audit trails, and documents are not lost. It reduces the time you spend on tracking and reporting training progress and other QMS elements like deviations, CAPA, complaints, etc. This allows you to focus your resources more effectively on important tasks instead of chasing paper. Finally, using a digital QMS reduces the overall cost of implementing a QMS over the long run.